The gear-driven structure in the milling cutter component of butt fusion welding machines offers distinct advantages over traditional chain-driven systems.
As we all know, the traditional chain drive has a simple structure and low manufacturing cost, but the chain is easy to wear and has a relatively short service life. In addition, the chain movement may generate noise and vibration, affecting the working environment and operating comfort.
Compared with gear-driven systems, chain-driven systems are less precise, which may affect the precision of the welding task.
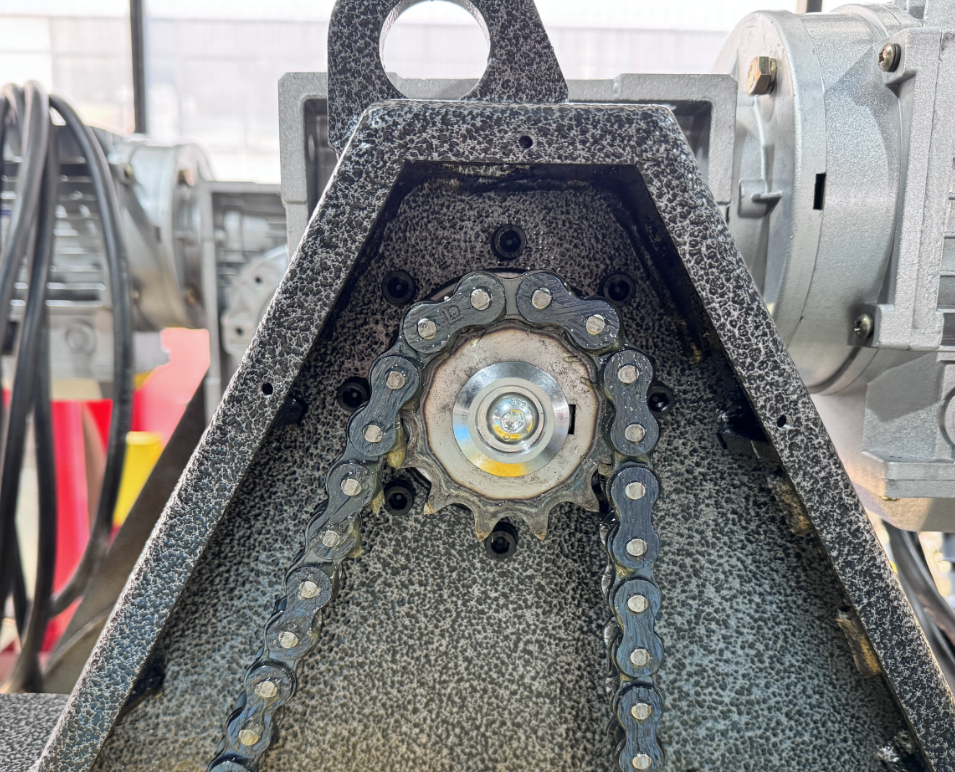
(Pictured are milling cutters for 450-800 MM hydraulic machines)
The gear mechanism ensures finer control over the milling process, resulting in smoother and more accurate welds. This heightened precision minimizes material wastage, making the welding process more cost-effective. Moreover, the gear-driven structure enhances durability by reducing wear and tear, translating to lower maintenance costs. This robust design not only improves the overall performance but also extends the lifespan of the welding equipment, providing long-term reliability for your welding operations.